In today’s tough financial environment, medical laboratories with effective Lean and Six Sigma improvement programs are showing the best financial performance
When Dark Daily wrote about how cost-cutting is now a major clinical laboratory industry trend last Wednesday, publication of that ebriefing triggered a flow of emails and commentary from readers far and wide.
Pathologists and medical laboratory managers who read Dark Daily tell us that they are facing painful decisions about where to cut. This is particularly true when labs cut expenses by reducing staff, laying off FTEs. This approach brings much emotional pain—along with the loss of valuable technical skills and extensive organizational experience that cannot be easily replaced.
Layoffs of Medical Laboratory Staff Is Bad Way to Cut Costs
Even the layoff strategy has limited benefit. It may reduce costs during the immediate budget cycle, but most clinical laboratories must handle a steady increase in the volume of specimens from one year to the next. Thus, cutting back on the number of skilled medical technologists during this budget cycle can mean that the laboratory does not have enough skilled labor to handle the increased volume of specimens next year or in following years.
This is the quandary facing all lab managers. How do they do more work with less money and fewer resources?
If a lab’s only strategy is to cut costs each year to balance a shrinking budget, then that lab organization is not likely to survive. It will either be shut down or merged into a financially stronger lab organization.
Effective Ways for Clinical Laboratories to Slash Expenses
On the other hand, every clinical laboratory manager and every pathologist has a proven way to meet the current challenge of shrinking revenue for lab tests, despite a growing volume of specimens flowing into their laboratory. The solution is to adopt the same quality management philosophies and methods that have been used by the world’s leading corporations over the past three decades.
Simply said, quality management, as taught by W. Edwards Deming, Taiichi Ohno, and others, is the established way to continually reduce the cost of your product, while simultaneously improving its quality. Unfortunately, few in healthcare—and this is particularly true of senior hospital administrators with responsibility for the clinical laboratory—understand the core concept that underpins quality management.
Yet, everywhere in our daily life we see examples of products today that deliver incredible performance at a price that is literally pennies of what was originally charged. It is only by adopting Deming’s principles and the quality management philosophy that certain industries have transformed our daily lives. Think of the $4,000 IBM personal computer of the early 1980s and compare that to the high-powered laptop sold for under $500 by multiple manufacturers today.
Remember the first-generation cell phones of 1986? At a cost of $3,000, it required a box to be installed in the trunk of your car, with the handset placed by the driver. Today, smartphones can fit in a shirt pocket, cost just a couple of hundred dollars, and do much more than simply allow you to place or receive a telephone call!
Use of Quality Management Methods Is a Sure Path to Reduced Costs
My point here is to remind readers of Dark Daily that every clinical laboratory organization can adopt the same quality management philosophies and methods that these other industries used to drive down the cost of their products, while improving the value it delivers to customers.
Imagine being able to produce—for just 10¢—a 12-analyte chemistry panel with enriched information to the ordering physician and making money on the 20¢ reimbursement from payers. Metaphorically, this is how personal computer manufactures and cell phone companies have lowered both their cost to produce the product and price at which they can profitably sell those products.
Does this interest you as a lab leader? If so, you can get immediate access to the training and knowledge you need to deploy these effective quality management approaches in your own laboratory. You can attend the seventh Annual Lab Quality Confab on October 1-2, 2013, in New Orleans. This is the clinical lab industry’s only conference devoted totally to quality management and the methods of Lean, Six Sigma, process improvement, and ISO 15189. Topics, speakers, and lab case studies can be found at www.labqualityconfab.com.
Lean as a Way to Achieve Substantial Cost Cuts While Protecting Quality
Next, there are other resources your lab can tap to acquire knowledge and expertise in Lean, Six Sigma, and process improvement. In last week’s ebriefing, we provided information about five independent laboratory management consulting companies with a multi-year track record in using these management methods to help their lab clients. They have been active and visible in teaching these techniques at lab industry meetings.
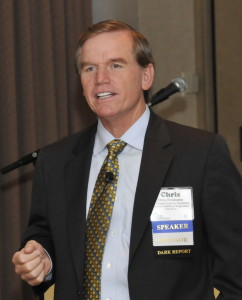
In the 1990’s, Chris Christopher was one of the first in the clinical laboratory industry to learn the techniques of process improvement, Lean, Six Sigma, and quality management and apply them to medical laboratory operations. Shown here speaking at a past Lab Quality Confab meeting, Christopher is currently the Vice President of Global Customer Solutions at Siemens Diagnostics.
We promised in this ebriefing to suggest in vitro diagnostics companies and laboratory informatics companies that have internal teams to provide consulting services to their lab customers that incorporate process improvement, Lean, and Six Sigma.
This very short list is made up of companies which were early to create their Lean/Six Sigma consulting services for laboratories and collaborate regularly with Dark Daily and The Dark Report to share their experiences, teach these techniques at public meetings, and encourage their most innovative clinical laboratory customers to speak in public about their labs’ successes with Lean and Six Sigma projects.
In particular, the companies listed below have actively supported the learning goals of the Executive War College, Lab Quality Confab, and similar laboratory management conferences. They have demonstrated their own commitment to quality management and are eager to share knowledge that can advance the management and operational performance of all laboratories, not just their own clients.
• Ortho-Clinical Diagnostics (OCD), a division of Johnson & Johnson, and its ValueMetrix Business Unit, Raritan, New Jersey. Website: www.valuemetrixservices.com
When it comes to Lean in clinical laboratory operations, OCD is the first-mover and pioneer. As early as 1998, OCD’s manufacturing facilities were using Lean to streamline workflow and incorporating Lean principles into the design of its medical laboratory analyzers. As early as 1999, ValueMetrix was established as a Lean/Six Sigma consultancy with the goal to help clinical laboratories and hospitals implement Lean methods and develop a Lean mindset and culture throughout the organization.
• Siemens Diagnostics, Tarrytown, New York. Website: www.healthcare.siemens.com/laboratory-diagnostics
Within this IVD manufacturer is a process improvement team lead by Chris Christopher. Since the late 1990s (when this group was part of Dade Behring), both Christopher and his lab clients have made presentations at lab industry meetings to share their knowledge and the power of quality management philosophies and continuous improvement.
• Sysmex America, Inc., Mundelein, Illinois. Website: www.sysmex.com/us/en/
Dating back to 2000, workflow redesign and the principles of W. Edwards Deming have been shared with lab clients across the United States. At the same time, Sysmex has been enthusiastic in encouraging its most innovative lab customers to make public presentations to share the knowledge about these process improvement techniques and their essential role in maximizing the productivity of automated systems and the entire laboratory staff.
• Sunquest Information Systems, Tucson, Arizona. Website: www.sunquestinfo.com
Following its divestiture from MiSys in 2007, Sunquest’s new executive team began aligning the functionality of its software offerings to better support those clinical laboratories utilizing Lean, Six Sigma, and workflow redesign in their everyday operations. It actively participates in public lab forums to share experience in how labs can more effectively use information technology to support continuous process improvement. It also supports its lab customers who want to share their labs’ experiences at improving workflow, reducing costs, and improving quality.
• Visiun (formerly Management Insight, LLC), Ann Arbor, Michigan. Website: www.visiun.com
Since the number of clinical laboratories adopting Lean and Six Sigma began increasing in 2003, Tom Joseph has been creating data analytics solutions that lab managers could use in process improvement redesign, for kaizen events, and in support of Lean projects. He regularly contributed to public lab meetings on these developments. Now the founder and CEO of his own firm, Joseph’s team is engaged in providing solutions that feed real-time analytics to managers in some of the nation’s leading medical laboratory organizations.
As a reminder, this list is made up of individuals and organizations that were early-adopters of quality management, Lean, and Six Sigma—and have maintained close communication with The Dark Report and Dark Daily about the successes of their laboratory clients going back five years, 10 years, and more. Their enthusiasm for quality management has been visible at each year’s Lab Quality Confab, for example.
Dark Daily’s Registry of Lab Industry Vendors Offering Lean Consulting
Because of the response we got from last week’s email from companies interested in being added to this list, we invite any company wanting to provide us with information about their consulting services involving Lean, Six Sigma, and process improvement to contact us using info@darkreport.com. We are interested in developing a public registry of these resources.
We are also interested in providing a public forum for your best-of-class laboratory clients to share their success stories in how they have used these quality management methods to cut costs and improve quality.
Come To Lab Quality Confab and Master Cost-Cutting Strategies
The entire clinical laboratory profession faces an extended period of falling reimbursement and less money for lab testing. For that reason alone, every lab organization and every lab industry vendor should have their best and brightest cost-cutters at the seventh annual Lab Quality Confab. This will take place on October 1-2, 2013, at the Astor Crowne Plaza Hotel in New Orleans. Visit www.labqualityconfab.com to see the topics and speakers.
For the modest investment of registration and travel expenses, attendees at Lab Quality Confab will get everything they need to immediately find sources of waste and unnecessary cost in their lab operations. Past attendees have been able to eliminate as much as $100,000 in unnecessary lab costs between their attendance at Lab Quality Confab and the end of the calendar year!
Dealing with the Clinical Lab Industry’s Toughest Challenges
It is essential that every clinical lab and anatomic pathology practice have a business strategy in place to deal with shrinking lab budgets, along with trained managers who can competently and quickly cut wasteful spending and improve the productivity of lab automation and laboratory staff. For that reason, this year’s Lab Quality Confab is likely to be the most useful educational and training resource available to those lab managers on your team who are tasked with managing costs and boosting your lab’s performance.
Reminder: any company wanting to provide us with information about their consulting services involving Lean, Six Sigma, and process improvement, please contact us using info@darkreport.com.
Related Information:
Speakers, Topics, Agenda for seventh annual Lab Quality Confab
Clinical Pathology Laboratories Use Lean to Design “Ideal” Blood Draw Sites and Work Flow
Clinical Laboratories in United States Show More Interest in ISO 15189 Accreditation
Equally significant is the fact that the majority of clinical laboratories owned by hospitals and health systems do not have managers who have acquired the necessary skills and knowledge to be proficient in cutting costs the right way—by identifying sources of recurring waste, then using quality management methods to deliberately eliminate those sources of recurring waste and errors while maintaining or improving the quality of services delivered by the lab.
Although I agree that Lean and Six Sigma as a process works well to reduce costs, I think the metaphor that relates to the personal computer revolution to a lab service is not accurate. That reference relates to Moore’s Law that states that the number of transistors on a chip will double every two years. And since the 80’s that has been mostly true. But also true is that pc manufacturing has moved to Asia that employ laborers at 30 cents an hour to make our beloved gadgets. These are the main reasons these devices are so cheap and powerful.
A lab’s product is not a device, but a piece of information that is derived from expensive labor costs, equipment and overhead. Much more so than that in China or India as it relates to technology companies.
You say you remind us Daily Dark readers that we should adopt these management philosophies to help drive down the costs of our products. So what are the costs of producing that lab result? The biggest cost is labor, benefits, health insurance, instrumentation/reagents, facility, executive salaries, and IT. That is most of it.
So like you say, imagine doing a Compmeta panel for a cost of 10 cents and being reimbursed 20 cents. Now, if I was presented with this problem and I worked for IBM Laboratories, my solution would be to perform all the lab work in South East Asia and pay the techs 30 cents/hr vs $30/hour. And reap all the benefits that all these tech companies do and make the shareholders rejoice!
We all know that reducing technologists is key to saving money, but like you say, that is problematic. As test volume increases, you can’t keep cutting techs. Yes, you will reap some benefit from advancements in efficiency of equipment, and in a way it is like Moore’s law in that instrument throughput can be increased and at the same time continue to reduce FTE’s. But this can only continue with an increase in the scale of operation. Core labs will have to become larger in scale and fewer, and staffed by less and less people to reap the benefits of advancement in technologies. This shift has been going on for decades. Hospital labs are dying, small labs will not survive, and I think we will see this accelerate in the next few years as the realization becomes clear to all that our health system costs are unsustainable.
In your example, for a 20 cent reimbursement for a chem panel to be true, you would not be able isolate that sort of reimbursement schedule just to laboratories. It would have to occur across all sectors of healthcare. For example, Imaging centers instead of being reimbursed hundreds to thousands of dollars for a CAT scan, would have to also accept pennies on the dollar for a scan. But, I don’t believe this will happen without a huge fight, as we all know the healthcare/ Big Pharma industry is a gravy train for many people. And lobbyist’s are too powerful.
So although Chris Christopher may have good information for all us in lab management to help reduce costs, will he really address the structural problems we have in healthcare? And that to change that structure so we can have that 20 cent reimbursement will mean crippling changes that no one wants to talk about. And that is… the massive controlled fraud and price gouging in all areas healthcare will have to end.
And just one example of this was an article in the front pages of the NY Times last month, that talked about this man who had a hip replacement done in Belgium for the fraction of the cost to have it done in the US. And the main reason discovered was price gouging. A good read. We have all seen astronomical lab bills, I know I have, and just scratch my head in wonder how long this can continue. Not very long, we will be forced to change.
In conclusion, there is a metaphor to the articles example about computers and what is going to happen to the future of the labs. In the near term we will continue to see larger centralized labs and consolidation. Equipment vendors will continue to improve technology and throughput, which will keep staffing at a minimum. But just like how main frame centralized computing has migrated to ipad’s and smart phones, so too will lab testing. Bio-sensors will bring the testing to the patient and bedside, and the results will be in the palm of your hand and not in some centralized lab. Centralized labs will remain only to be performing esoteric testing, but in essence..gutted.
That future I believe is only 10 years away, and will be the ultimate in LEAN.
Thanks