Savvy medical laboratory managers conduct internal audits of processes involved in deficiency citations so they can uncover how deficiencies occur and help eliminate recurrences
One trend that places clinical laboratories at risk involves increased regulation of lab processes, along with more thorough accreditation inspections. Compared to past years, both developments mean more ways for lab assessors to find greater numbers of deficiencies.
However, leading laboratory accreditation and quality improvement experts say that many deficiencies could be avoided if lab leaders conducted their own internal audits and continuous quality improvement projects ahead of visits by accrediting authorities.
In an exclusive interview with Dark Daily, Randall Querry, Director of Government Relations at the American Association for Laboratory Accreditation (A2LA) said, “Clinical laboratories can do a better job of preparing for the external assessment by doing an internal audit. That is, watching personnel perform tests and noting if they aren’t following the same sequences that standard operating procedures address before the external assessors arrive.”
A2LA is one of the primary accrediting bodies with authority from the Centers for Medicare and Medicaid Services (CMS) to accredit medical laboratories relative to Clinical Laboratory Improvement Amendments (CLIA). Others include:
- COLA;
- College of American Pathologists (CAP); and
- The Joint Commission.
“This doesn’t have to be an ‘us against them’ exercise. We are all in this together for continual improvement and to ensure we’re doing a better job at the end of each day—that we have had a win,” said Querry said.
How Should Clinical Laboratories Conduct Internal Audits?
So, what is the best method for clinical laboratory leaders to conduct their own audits of operations and avoid citations of deficiencies?
Lucia Berte, President of Laboratories Made Better, suggested medical laboratories should “Pick a sequence and follow it through.” In the Dark Daily interview, she suggested labs should focus on:
- The sequence of receiving samples in the laboratory to make certain they are properly accessioned, processed, and distributed;
- Steps to setting up and running an analyzer; and
- The process of ensuring tests’ critical values are reported to ordering clinicians and how reports are made.
An internal audit may suggest areas where the clinical lab is not on target to meet regulatory and accreditation criteria. Or, the lab may discover what Querry calls “gray areas”—places where criteria are currently being met, but a trend suggests there could be problems down the road.
“And in those cases, it’s always good to identify areas of improvement for preventative action. They may not be a top priority—such as a deficiency—but the areas are on the radar screen as something to address to prevent it becoming a worsening problem,” Querry said.
Quality Improvement Processes to Address Deficiencies
Berte notes that citations in one area of the lab may suggest the need for continuous improvement projects across all laboratory departments or sections. For example, an accrediting body may cite chemistry for a deficiency while hematology and other departments do okay. However, that determination can be deceiving.
“There is always an underlying process. And the better question for the clinical laboratory is ‘can we make an improvement project out of this that can solve this problem not only for the area where it was cited, but perhaps prevent this problem from occurring in other lab [departments] prior to the next external accreditation assessments?’” Berte said.
Lack of Uniformity among a Clinical Laboratory’s Departments
Berte says a common deficiency is “lack of a uniform competency assessment program” for staff throughout the lab. Assessors expect laboratory departments to have the same competency assessment in regard to processes, records, and the way documents are created, she explained.
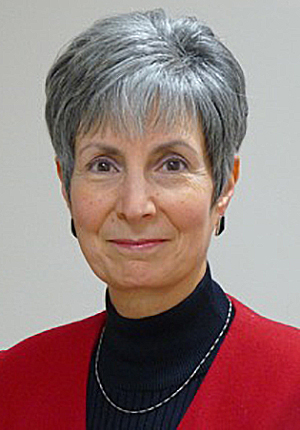
Competency-related Citations
Berte also said competency-related citations may happen when documents read by auditors are not in sync with what the officials see in the clinical lab during inspections. “People not doing things in the order in which things have to happen. That’s the disconnect.”
Querry, speaking from the perspective of an assessor, adds, “We see a discrepancy and ask—do they have the appropriate work procedures with them at the workstation? Is it accessible? Where is this discrepancy? We identify it and then it’s up to the lab to address it—in training, and between the written procedure and the process.”
Consistency, he says, is important especially in organizations where staff rotate among lab areas and different shifts.
Quality System Essentials for Clinical Laboratories
The website for the Clinical and Laboratory Standards Institute (CLIA) states that implementing a quality management system in the lab involves use of “quality system essentials (QSEs).” QSEs are key to lab workflow, communication, and training. They include documents and records management, assessments, and continual improvement.
Querry emphasizes that trying to predict what the hot citations may be in 2020 is not as important as focusing on the technical competence of the lab and its resources.
“We are not out to play gotcha. We are going in there, looking at all the systems, and doing a sampling of testing in various departments of the lab. It’s up to the lab to show us it is technically competent to perform those tests. And they have the equipment and records that the equipment has been checked and calibrated and maintained. We have an examination process,” he said.
Experts agree, clinical laboratories that prepare for external assessments with internal audits and continuous improvement programs may reduce deficiencies during inspections.
—Donna Marie Pocius
Related Information:
Top Laboratory Deficiencies Across Accreditation Agencies
Implementing a Quality Management System in the Laboratory
Lab Quality Confab hosted by The Dark Report
25th Annual Executive War College on lab and pathology management April 28 – 29, 2020
Greetings,
Thanks so much for sharing.
We at MedLabs Consultancy Group in Amman-Jordan (with 41 branches) believe that a yearly unannounced internal audit is very beneficial. The checklist evolves every year, it is discussed in a workshop before the actual unannounced audit. I will be more than happy to share our experience with any colleague who is interested.